Forwell - Kirti Weld Controller
1Why the controller is required on the machine ? Can’t we make it with simple timer?
Spot welding machine consists of transformer capable of delivering high currents. This high current melts the sheets through its flow. Higher current than required will melt all metal away leaving a burnt spot and lower current will not make the spot. The controller accurately controls “time” and welding current required for good weld. The typical welding times are very short i.e. 6 to 20 cycles (1cycle=20 millisecond or 0.020 second).
Welding current is controlled by varying firing angle of the thyristor which is in circuit with transformer as a variable switch.
Normal timer cannot do the timing functions as “welding time” needs to be synchronized with AC phase. Controller is not just timer but it controls thyristor providing proper firing angle signal at exact instant. (is it – ‘at exact spot’ ?)
2What is secondary feedback control?
The secondary feedback controller takes feedback from secondary of the machine where currents are of the order from 6000amps to 15000amps or more( depending on component) . This feedback is sent to controller for processing, controller applies correction by changing firing angle, thus the machine operates in closed loop.
This means if you program machine to deliver 10KA it will deliver the specified current with feedback processing and adjusting the firing angle of the thyristor.
3What is ‘weld monitor’ ?
Weld monitor is a system which measures current flowing during welding process, displays the values and gives decision about weld quality. This equipment needs to be externally attached to welding machines. Weld monitor can not ‘correct’ the values.
This facility is inbuilt with FORWEL-Kirti along with correction of values, display of real time current, its %deviation with set parameter, and printout / net working functions (optional).
4Why I should buy FORWEL-Kirti over other make?
There are many reasons to go for FORWEL-Kirti you can compare yourself. If you want to get free trials of the same for your satisfaction contact KIRTI .
Service support and availability of spares will make your controller running on machine forever unlike other “unserviceable “make.
All this is possible at lower cost and better quality with FORWEL-Kirti.
5I have 150 KVA seam welder which model will suit to my machine ?
FORWEL AK54 can be retrofitted on all KVA machines.
Model selection is on fixing method of controller i.e. horizontal or vertical. If your earlier controller is vertically mounted AK54 V 220-RY will be suitable for you.
6I have foot pedal operated machine, can I retrofit the FORWEL-Kirti controller over it. ?
Controller controls firing angle of thyristor assembly, most of the foot operated machines work with electric contactors. FORWEL-Kirti can not control contactors. Pressure is given by foot and springs. It is not advisable to retrofit FORWEL-Kirti with pedal machines.
7I have pneumatic spot welder of XYZ make, what changes are required for retrofitting ?
For any make of spot or seam welder, FORWEL-Kirti replaces existing controller only. Other items like valve, thyristor are used as it was present earlier.
8How long it will take for change ?
Retrofit process consists of
1. mechanical fitting of controller
2. mechanical fitting of tower lamp/ buzzer(optional)
3. electrical connections.
4. programming controller for the application.
Overall it takes one hour for the change.
9How programming differs from my earlier controller ?
If you are operating voltage compensation type C-Mos or Digital controllers programming is different in terms of current setting. In FORWEL-Kirti Controller you can directly input “current” required for the welding operation these values are typically 8 KA~ 15KA depending on job thickness. In Voltage type controller we input firing angle as “% heat”
The “% heat” values may be 60 % to 90 %.
10How we can confirm zero rejects on spot welding using FORWEL-Kirti Controller?
Installing FORWEL-Kirti alone will not give zero defects. The process needs to be validated for lowest and highest current values, the machine should be in good condition to deliver required current in required time. Machines should be free from internal “shorts”.
It is possible practically to achieve zero defect parts with proper discipline. The validated process with FORWEL-Kirti controller can give alert on defective part as soon as it is produced, operator should keep such parts in rejection bin.
11How the controllers can go bad?
Wrong connections are major reason for damaging controller ( of any make ). As controller handles high line voltages it is dangerous to connect wires at wrong terminals.
All controllers are protected against spikes, high voltages transients. There are some instances of burning off terminal of back panel. This happens in abnormal cases when thyristor of the machine shorts, due to some external reasons.
If the controller is properly isolated by “isolation transformer “ ; most of the malfunctions can be eliminated. This isolation transformer provides 220V for control power of the controller.
All such cases are repairable at KIRTI. This means your controller can not go out of service anymore.
Download Kirti Support App from Google Playstore
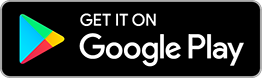